Company News
Application of vision inspection systems for quality control in soft pack production
Date:2017-03-17
Source:Samsun Technology
In today's flexible packaging printing market, competition is extremely fierce. In addition to price being a consideration for customers, customers also pay great attention to the quality of the product. The quality of the product, reliability, stability, production costs, directly affect the competitiveness of enterprises in the market, affecting the effectiveness and survival of enterprises. As a person in charge of quality management, how to ensure high quality factory, especially low-cost products how to ensure high quality factory, very difficult. This article mainly shares some personal experience, to the soft package industry friends throwing bricks to draw in the jade.
Difficult problem: manual detection of defects - low efficiency, high customer complaints
Our company is divided into a production workshop and a post-processing workshop. Production workshop to do printing, after processing workshop to do sub-rewinding, slitting processing.
First, analyse the situation in our production workshop. We currently have a fast printing speed, which can reach about 200m/min; we rely on still images and occasional observation of strobe lights to control production quality.
We have purchased the most advanced printing presses in the industry and employed experienced operators; tried to use good quality raw materials; and introduced advanced 6S management. However, no matter how advanced the printing equipment is, how high the level of workers' operation, how strict the control of raw materials is, and how standard the management is, the emergence of various defective products cannot be avoided.
Secondly, to analyse the situation of our post-processing workshop.
1, we carry out manual inspection on the rewinder at a speed of 150m/min. The manual inspection is carried out by means of a hand-held strobe light.
2, after detecting the defect, stop the machine and manually control the rewinder to reverse and find the defect.
3、After slitting, handle small roll defects.
The biggest headache for the post-processing workshop is the factory quality inspection. We try to reduce the speed as much as possible, but for occasional defects basically can not be detected, and even some continuous small defects are missed. Moreover, the workers' inspection results are sometimes good and sometimes bad, and the standards are not uniform. The workers always fail to satisfy us and complain about the tiredness of their eyes and the intensity of their work. But our customers are becoming more and more demanding, and products that were very well accepted by our customers two years ago are now the subject of frequent complaints.
Quality control breakthrough - visual inspection system
How to improve the yield of the production process and how to improve our factory quality inspection process became the bottleneck of our factory production. The printing vision inspection system came into being, which can replace manual inspection with machines.
Solution 1: In-line inspection system on the printing press to control the quality of the label printing process, with an audible and visual alarm when defects are detected.
This solution focuses on controlling defects in the printing process, finding the cause of defects immediately and rectifying the root cause of the problem. It can effectively reduce the occurrence of defective products.
Solution 2: Visual inspection system installed in the slitter, rechecking machine and other equipment, after the detection of defects, can be uncovered and cut to join the material, in the label factory before the quality of the product testing. This solution focuses on controlling the quality of the factory to ensure 100% qualified products leave the factory.
In line with the customer first principle, we felt that ensuring the quality of the product leaving the factory was of paramount importance and chose a second solution, installing an automatic inspection system on the rewinder for a trial period. During the two-month trial, the visual inspection system not only greatly improved the inspection speed and reduced labour costs, but also the inspection accuracy was much higher than that of manual labour, and the customer's satisfaction with our products increased significantly.
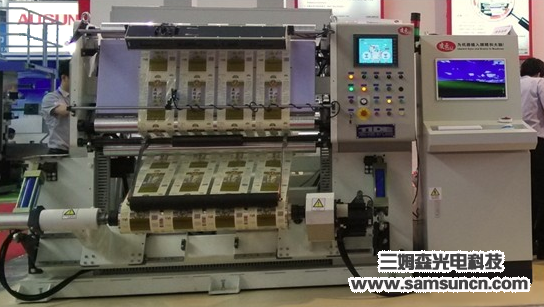
Figure 1 Rewinder with vision inspection system
The vision inspection system uses the world's most advanced line array high-speed imaging ultra-high definition camera to take continuous photos, then its self-developed inspection software analyses the photos to find defects and feeds the results back to the rewinder, allowing the rewinder to stop the defects at a specified locations, thereby rejecting them. The advantages over manual labour are.
1、Standards are strictly uniform and different products can be tested differently, for example
Quality inspection test setting values are set as follows: Grade A - stricter; Grade B - average; Grade C - looser
Level A: "Knife line - (70%-90%)" "Ink spot - (70%-90%)" "White spots - (50% - 70%)" "Off-colour defects - (40% - 60%)".
Grade B: "Knife line - (60%-80%)" "Ink spot - (60%-80%)" "White spots - (40% - 60%)" "Off-colour defects - (30% - 50%)".
Grade C: "Knife line - (50%-70%)" "Ink spot - (50%-70%)" "White spots - (30% - 50%)" "Off-colour defects - (20% - 40%)".
2. high colour resolution, 100% full inspection, never fatigue.

3. rich defect browsing and analysis functions.
When the inspection is completed and the defect data is saved in the inspection system, the inspection software has the following functions for processing the data.
Printing of defects according to batches.
can be divided into list and view mode for defect browsing.
the possibility of outputting reports (defect schedules, defect distribution maps)
statistical functions for long-term inspection.
LAN shared viewing of defects.
Managers can view defect data remotely, so that they can understand production quality without having to visit the workshop. The process engineer can use the long-term defect statistics function, defect distribution, etc. to find the most dense occurrence of defects and thus improve the production process, etc.
Our company has introduced a visual inspection system, which is retrofitted to the free rewinder, with an inspection speed of 250 m/min and an automatic stop when defects are encountered, making it efficient and fast. Customers with high quality requirements have now all been replaced by visual inspection systems. The number of customer complaints received is almost zero.
Some wise domestic flexible packaging companies have been at the forefront of the industry, taking the lead in introducing a variety of automated equipment to replace traditional manual labour, reducing labour costs and improving production efficiency. Our country is a big printing country and I hope that some of my experiences can bring help to friends in the industry.