Company News
Measurement and control of samsonite-case study on appearance inspection of semiconductor conductor frame
Semiconductor products are ubiquitous in our lives, if there is a small error in the production process, it may cause irreversible impact. For semiconductor manufacturing enterprises, the word-of-mouth products even more than the value of the product itself. Therefore, word-of-mouth has become the decisive criterion for consumers to buy semiconductor products。
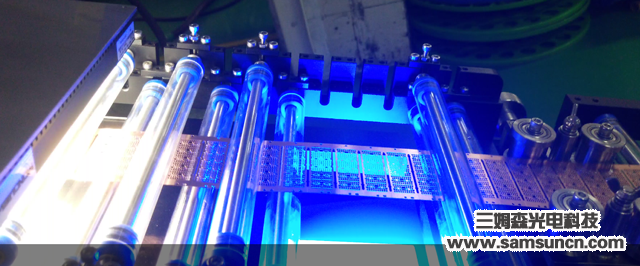
Increasingly sophisticated detection systems:Testing requires multiple products to achieve a strong compatibility, the same algorithm function can be the completion of the two-station testing requirements, to complete such a strong compatibility of software algorithm is not easy. For a visual inspection system, the compatibility of the software algorithm needs to be able to detect not only the different inspection requirements of different work stations, but also the different inspection speed of different products, one of the fastest detection speed is 1 min / 500 times of stamping two stations in the case of testing at the same time to complete. 3 Musen Muwe Measurement and Control Division (hereinafter referred to as "Muwe measurement and control") the intelligent detection system can meet this demand
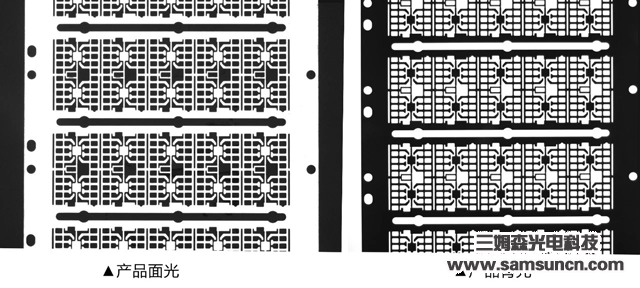
monoview measurement and control to help you solve the problem
The traditional practice of the project testing, by artificial time for product sampling inspection, so there will be many problems as follows:
1、 People in the long-term work easy to produce fatigue missed sampling inspection, can not find defective goods in time, resulting in a large number of scrap
2、Product variety, need to invest a lot of manpower and material resources to complete this thing. And it didn't work out so well.
3、Because manual testing can not be in the state of production movement testing, shutdown can be tested. This affects the production of products, resulting in production can not be completed on time.
Manual spot checks are prone to errors, and even minor product defects can lead to a loss of confidence in the manufacturing process and the overall quality of the product, or even a questioning of the entire manufacturer's brand, leading to consumer resistance to buying desire. This is fatal for the manufacturer.
In order to solve this series of problems, manufacturers to find different suppliers to provide different visual inspection system. Finally, the vision intelligent detection system of Muwe measurement and control was successfully selected by them. After the introduction of the detection system, not only the production capacity is greatly improved, but also the quality is several times better than before
Muwei measurement and control not only uses the first-line brand accessories, but also a particularly powerful and intelligent detection system, a function can be compatible with a number of detection of different functional requirements of the workstation (appearance detection, size differences) . A good system can help customers solve many problems, to the highest productivity, risk reduction to the minimum。
Here's how the system works:
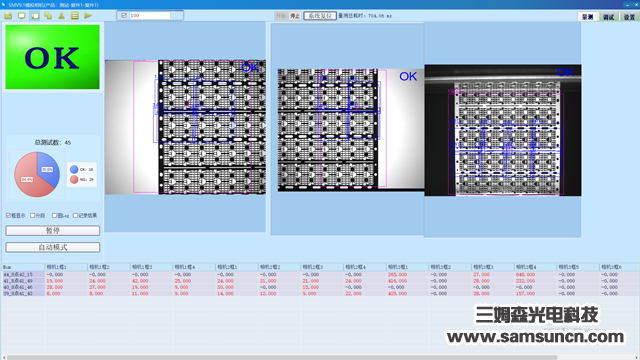
The display interface of the test results of 2 workstations and 3 cameras is OK
Same area backlight Algorithm display effect page:
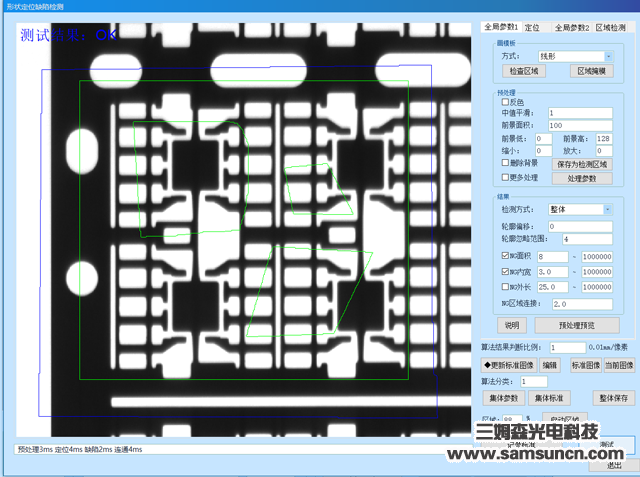
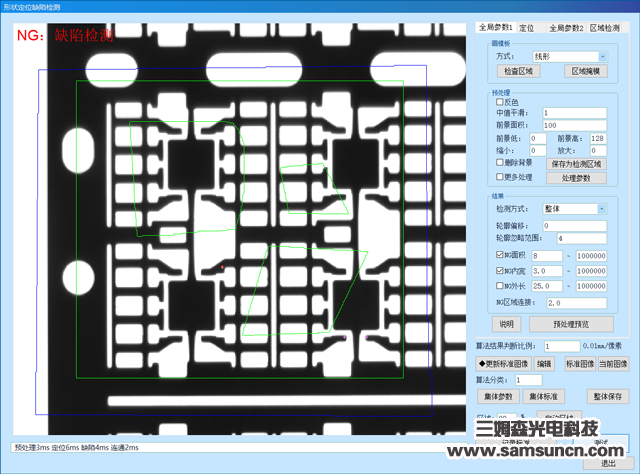
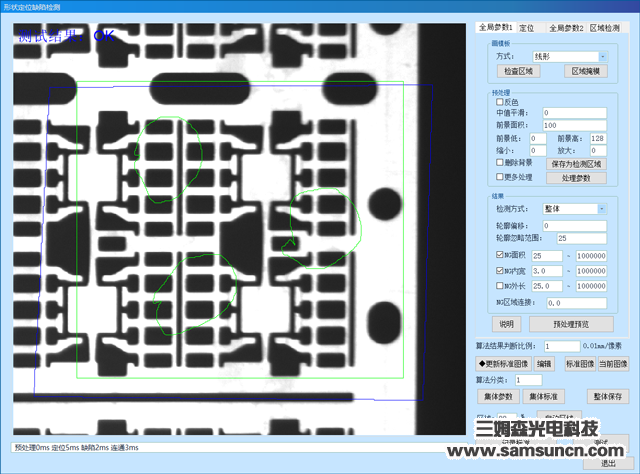
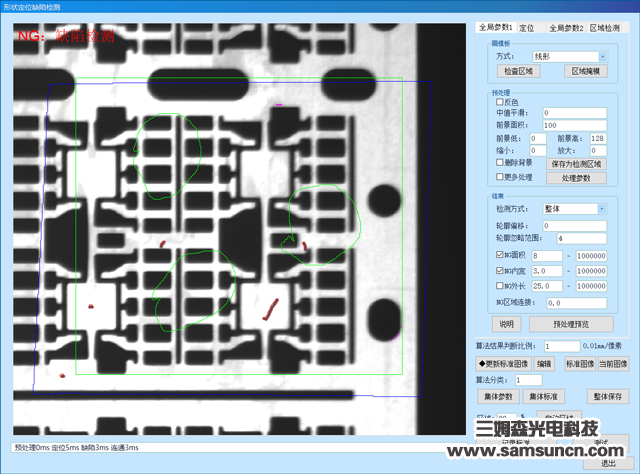
Ok figure 1 and Ng figure 1 are Surface Light, & Lt; span style"color: # FF0000;"& GT; Test Product Crush, pad, scratch. If there is oil on the surface of the product, do not test for Ng, and the test accuracy is less than 0.02 mm.
Field Test results
Through several sets of pictures and video understanding, I believe that friends also understand. Start from the bottom of the development of software companies, through the long accumulation of technology and hone, can bring more security and effect to customers. There are thousands of systems, each of them have advantages, but more importantly, how we choose a reliable, strong company to serve you, is the most important.