Technical Articles
The main problems of line laser 3D camera and the corresponding solutions
Linear laser scanning is widely used in industrial vision inspection, such as Pin Pin Pin Pin inspection, flatness inspection, straightness inspection, etc. . However, there are some problems in the 3D camera of Linear laser scanning, the following is a brief description of the main problems and the corresponding solutions:
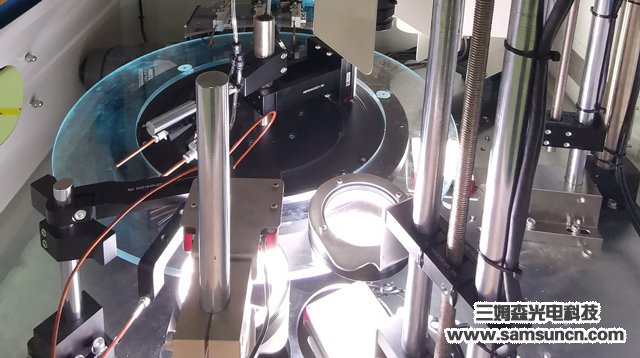
1. In the sensor system:
1 the focal depth limit of the incident beam: When the General Gauss beam is focused on the incident beam, the spot size will increase with the measurement range and the defocus will increase, the system is difficult to meet the requirements of high resolution and large measurement range. When the CCD is used as the detector, the corresponding improvement method is to take the center position of the rectangular pulse of the CCD output by the center of gravity method, while the PSD is used as the detector to avoid the influence of the light spot shape, but it still affects the resolution of the system. In some literatures, non-diffracting beams are used as light source to solve this problem.
2 The aberration of the optical system makes the beam from any point on the object pass through the optical system, can not converge to a point, but form a dispersion spot or make the image can not strictly show the shape of the original object. The corresponding improvement method is to consider the factor of aberration in the design of the receiving Lens.
3 The relationship between nonlinear inputs and outputs. The improved method includes making the look-up table by the better calibration method, and then getting the concrete object displacement value by looking up the table in the course of measurement.
2. For the object to be measured:
1 due to the influence of the shadow and dead zone caused by the inclination of the surface to be measured on the measurement, the corresponding methods are: A two way scanning triangulation in which the measured object is scanned from both directions using diffraction light from the Acousto-optic modulator, using a single light source, two detectors, and finally a laser double triangulation in which data are fused.
2.The sensor can not receive the reflected or diffuse light due to the step of the surface to be measured, such as hole or slit. The solution is an optical triangulation sensor with rotational symmetry.
3 The difference of color, material, roughness, optical property and surface shape of the measured surface results in the different reflection and absorption of light on the surface of the object when the same light source is incident, especially because of the roughness and refractive index of the object surface and other factors, the imaging Facula or stripe has aberration. The improved method is that the measuring plane determined by the incident lens of the sensor and the optical axis of the receiving lens is parallel to the texture of the surface to be measured, so that enough light intensity can be received and the measurement resolution can be improved.
4 High specular reflections cause speckles to corrode the image points. The solution is to spray a layer of non-smooth coating on the metal surface to reduce the reflectivity of the metal surface, and to use the linear polarized light as the light source, the phenomenon that the parameters of the linear polarized light change with the specular reflection of the metal surface.
3. In the aspect of external environment:
1 environmental noise such as temperature, humidity and mechanical vibration will affect the system parameters in triangulation. In addition to improving the precision of the system by better calibration method, the anti-noise performance of the system can be improved by using double non-diffracting beams as light source, and the system can be designed by using double-sided double-beam system with complete symmetry.
2 The interference of external and ambient light can be solved by using modulation circuit when PSD detector is used, using polarized light as light source, and using narrow band filter to isolate ambient light.
According to the problems and improvements of laser triangulation, the author thinks that the development trend of laser triangulation can be summarized as follows:
1.By introducing new optical devices, advanced sensor technology and accurate measurement algorithm, the measurement accuracy and speed are improved continuously, and the robustness of the measurement system is further enhanced
2.The hardware architecture of the system is improved, such as multi-sensor information fusion, multi-light source, multi-sensor information fusion, better achieve depth information acquisition;
3.By combining with the intelligent control system, a better and faster processing algorithm is developed to achieve the maximum degree of photoelectric triangulation of flexible measurement.